the problem
Dirt, dust, oils and waste build up can reduce the lifespan of printing equipment. Contaminants can increase the risk of expensive unexpected breakdowns and incidents such as fires.
Hard -to-reach areas can often be neglected deep within the machines with normal cleaning, but with dry ice we can clean those areas to a high standard with the added advantage of not needing to dismantle machine components. This helps massively in reducing downtime and saves money by getting the machines back up and running quickly.
- Printing presses
- Ink wheels
- Feeder units
- Drums
- Rollers / Grippers
- Gears
- Machine walls
- Letterpress
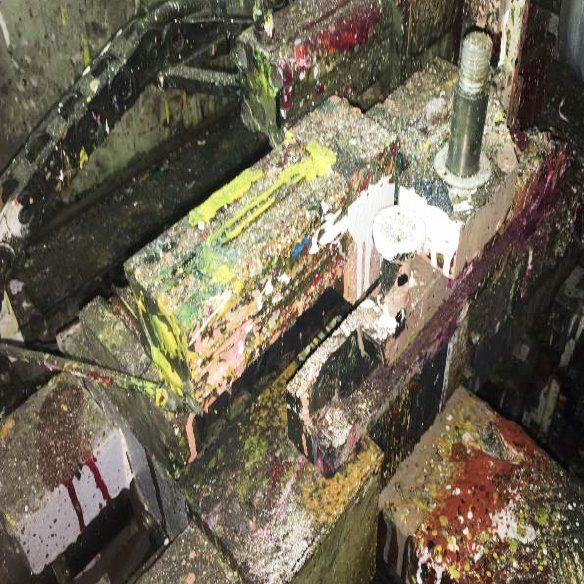
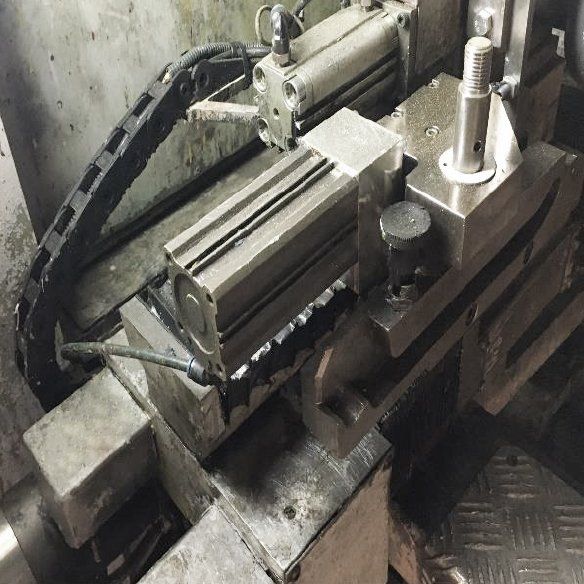
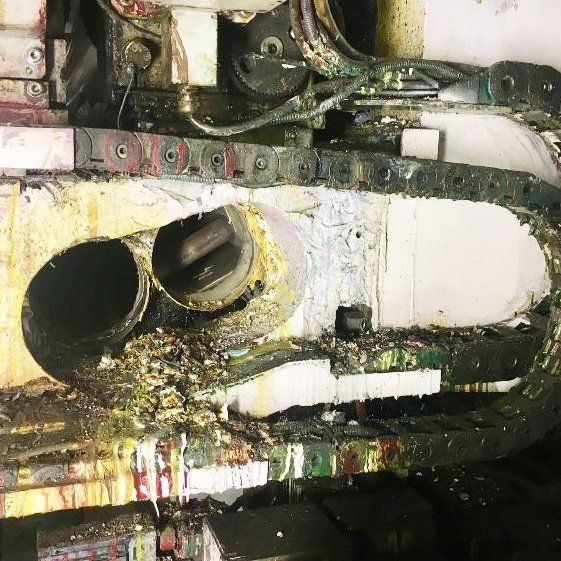
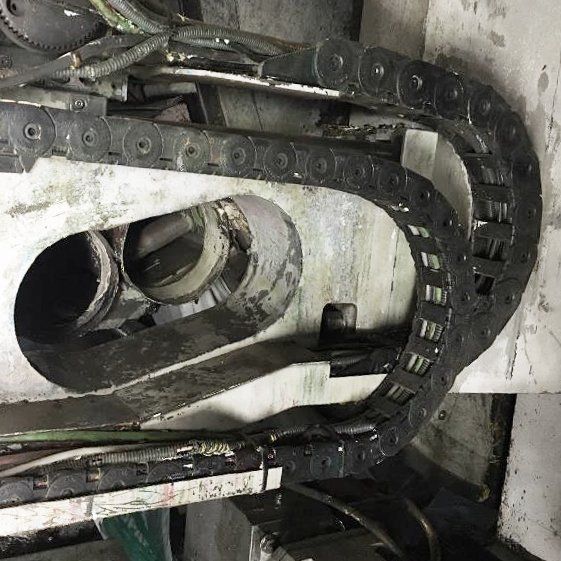
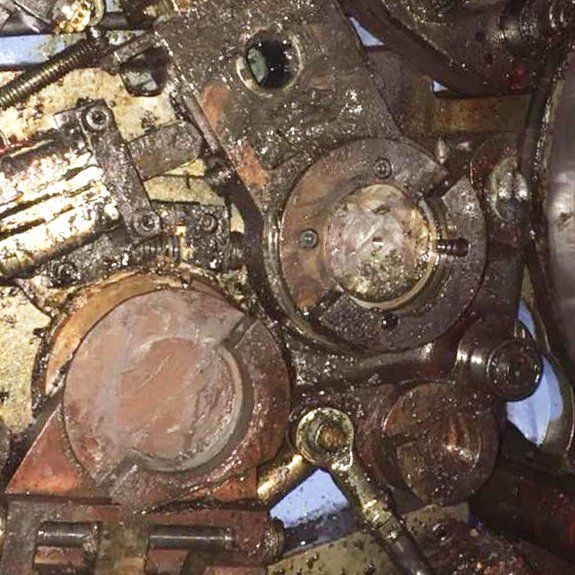
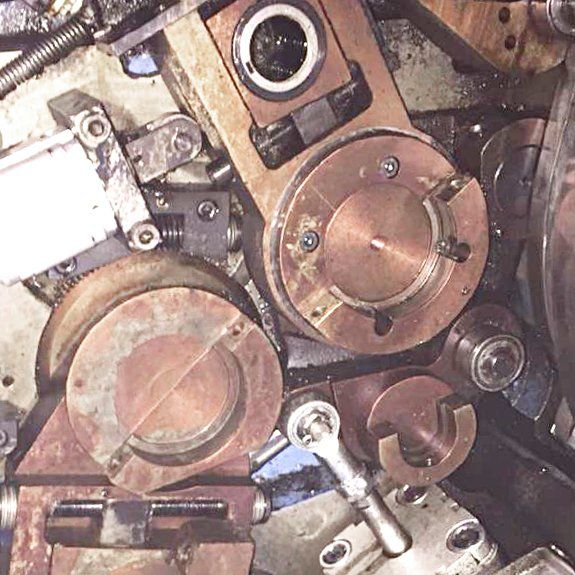
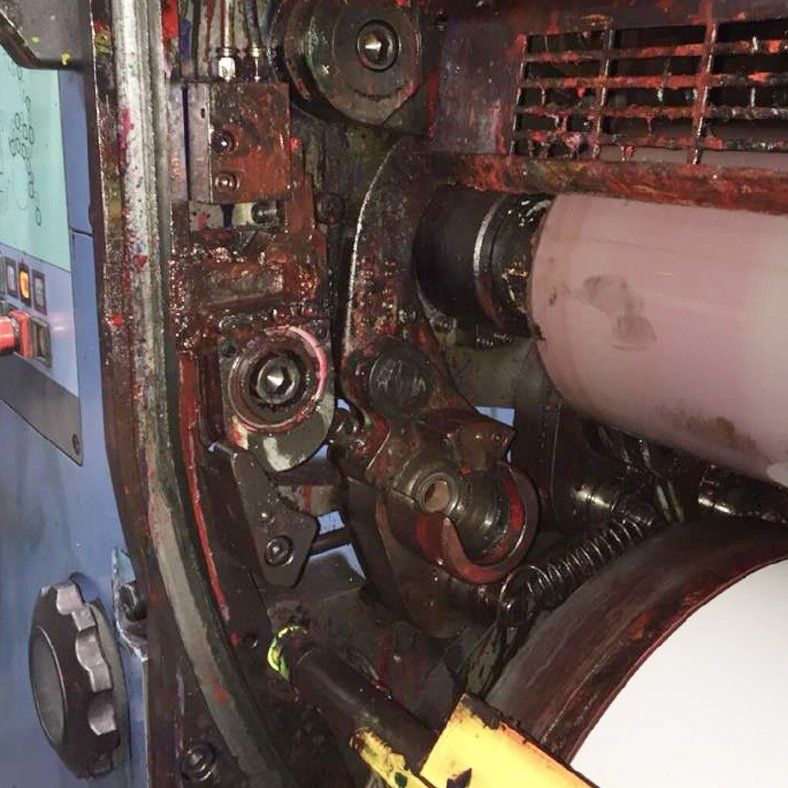
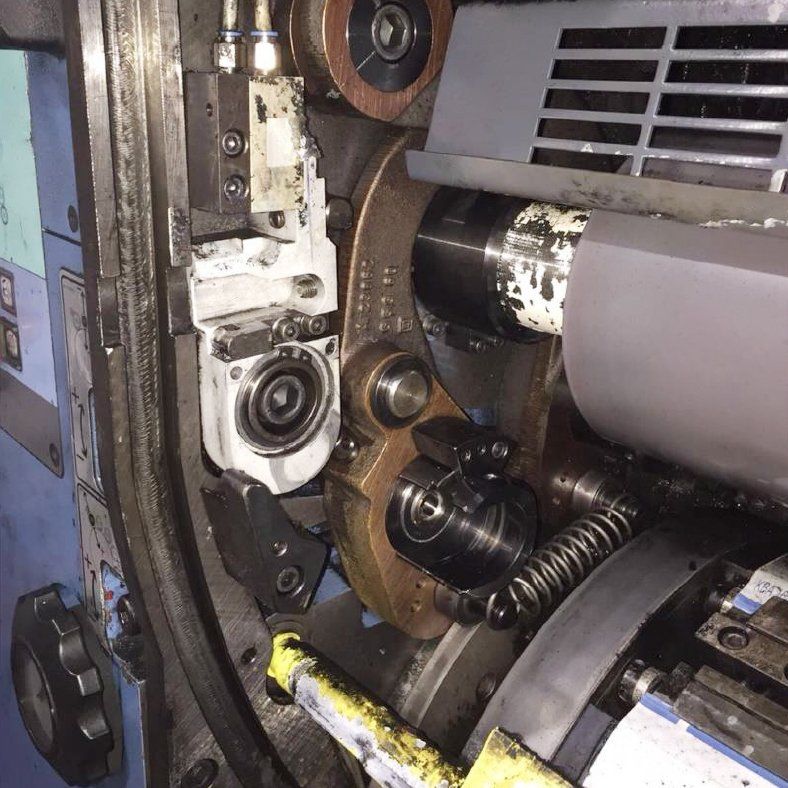
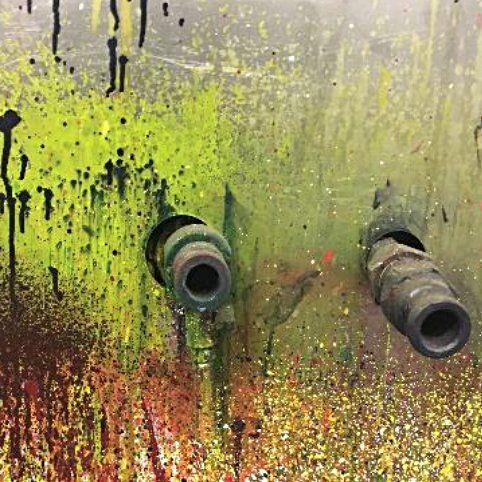
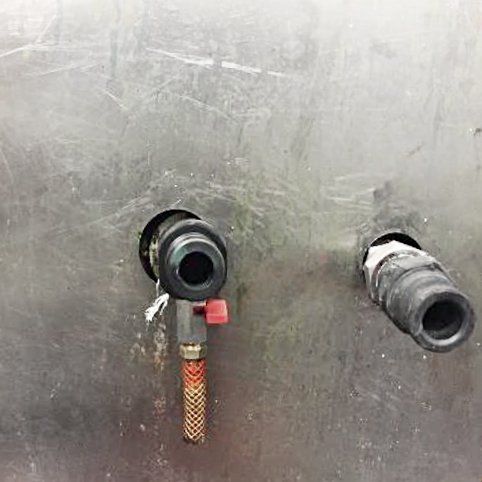
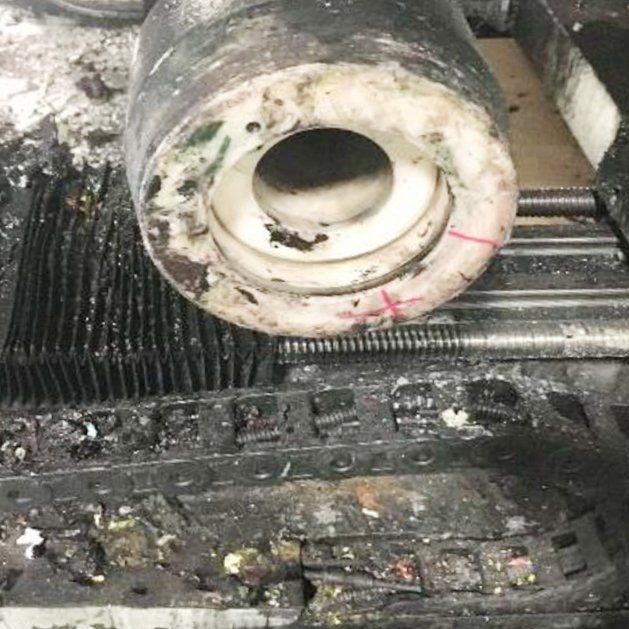
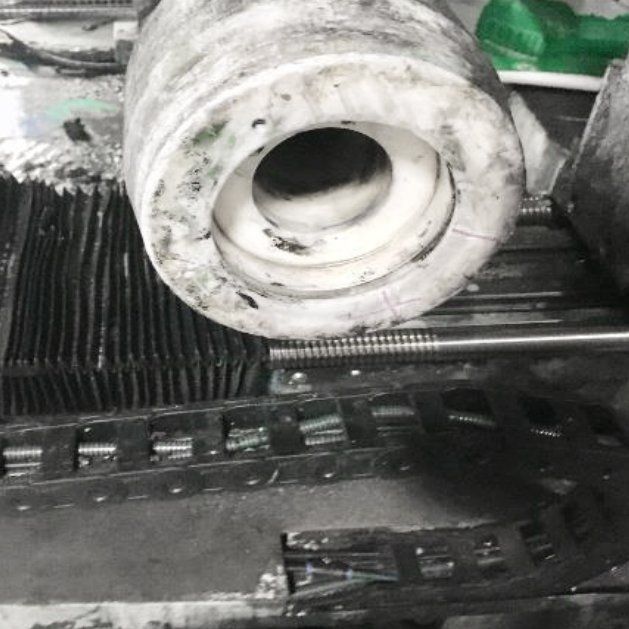
the solution
- NO RISK TO STAFF OR MACHINERY
- DRY SOLUTION - SAFE FOR WATER-SENSITIVE ENVIRONMENTS
- KILLS BACTERIA
- NON-ARBRASIVE
- GREEN CLEAN/ENVIRONMENTALLY FRIENDLY
- CLEANS FASTER AND MORE EFFICIENTLY
- CAN BE COMPLETED ON-SITE
- DOWNTIME DRAMATICALLY REDUCED
- PRODUCTION TIME INCREASED
- REDUCED COSTS
- PRODUCTIVITY AND APPEARANCE OF THE MACHINERY ENHANCED
- EXTENDED LIFESPAN OF EQUIPMENT
the benefits
keeping on top of it...
With a three or six monthly maintenance plan we can keep on top of your environments and have them running efficiently all year round, every year.